Осуществление процессов резки с применением плазменного аппарата Плазар АП022
г. Москва 2004 г.
Предисловие.
Настоящее пособие предназначено для руководства пользователю плазменным аппаратом «Плазар» АП022 при отработке технологических процессов резки материалов. Пособие является развитием соответствующего раздела «Технического описания и инструкции по эксплуатации» плазменного аппарата. Пособие рассчитано как на непрофессиональных пользователей, так и на профессиональных, но впервые имеющих дело с аппаратом «Плазар».
Введение.
Водоплазменная резка – это один из способов термической резки, т.е. технологический процесс, при котором отделение частей разрезаемой заготовки производят посредством использования концентрированного нагрева, создаваемого специальным источником теплоты – плазмотроном (плазменной горелкой), использующим воду в качестве плазмообразующей среды. Для плазменной резки используют так называемые сжатые дуги, отличающиеся интенсивным плазмообразованием в результате обдува дуги соосным или вихревым потоком газа. В связи с этим плазменную дугу формируют в специальном устройстве – плазмотроне (плазменной горелке), состоящем из двух основных элементов - электрода и формирующего сопла, через канал которого пропускают столб электрической дуги вместе с плазмообразующим газом, подаваемым под определенным давлением. В плазменной горелке «Плазар» ГП02 использована дуга косвенного действия (рис. 1), которая возбуждается и горит между электродами, которые не связаны с обрабатываемым материалом. Катодом служит электрод плазмотрона, а в качестве анода используют его формирующее сопло. Объект обработки не включен в электрическую цепь. Столб дуги расположен внутри плазмотрона: начинается на электроде и заканчивается анодным пятном на внутренней поверхности канала сопла. Под действием давления плазмообразующего газа, подаваемого в камеру плазмотрона, столб дуги проходит через канал сопла, а анодное пятно перемещается по его внутренней поверхности лишь до выходного среза канала сопла плазмотрона. В связи с этим плазмообразующий газ и его плазма лишь на коротком участке контактируют со столбом дуги, а затем существуют независимо от него. Этот вид резки называется резкой плазменной струей. Особенность технологии плазменной резки состоит в том, что плазменной струей, локализованной на малом участке поверхности разрезаемого материала, не только расплавляют материал, но и удаляют расплав из зоны реза высокоскоростным потоком. Дугу косвенного действия используют для обработки любых материалов: как проводящих электрический ток, так и не проводящих электрический ток. Плазменная резка аппаратом «Плазар» АП022 имеет свои конкурентные преимущества по сравнению с другими видами термической резки материалов. А именно:
- не требуется подготовки листа к резке (лист может быть окисленный, покрытый ржавчиной, краской и т.п.);
- небольшая ширина реза позволяет сократить припуски на обработку детали;
- малая ширина зоны термического влияния;
- резке поддаются практически все материалы (медь и ее сплавы, алюминий и его сплавы, низколегированные стали, нержавеющие стали, в том числе жаропрочные, а также неметаллические и композиционные материалы);
- максимальная толщина разрезаемых листов, мм:
- низкоуглеродистые и низколегированные стали – 7,0;
- алюминий и его сплавы – 4,0;
- скорость резки при толщине листа 1,2 – 3,0 мм, мм/мин:
- 08КП (2мм) – 200 – 360
- 12Х18Н10Т (3мм) – 70 – 120
- АМг (1,2мм) – 150 – 200
РИС.1. Схема плазменной дуги косвенного действия и ее участки: а - закрытый; б - сжатый; в - плазменная струя; г – факел плазмы.
1. Характеристика плазменной дуги и плазмообразующей среды.
Струю плазмы получают путем обжатия столба дуги в канале сопла. Под воздействием стенок канала сопла и струи плазмообразующего газа, столб дуги сжимается, его поперечное сечение уменьшается, а температура в центральной части столба дуги повышается до 10000 К. В результате внутренний слой плазмообразующего газа, соприкасающийся со столбом дуги, превращается в плазму, а наружный слой, омывающий стенки канала сопла, остается сравнительно холодным, образуя электрическую и тепловую изоляцию между потоком плазмы и каналом сопла. Этот охлажденный слой газа препятствует отклонению столба дуги от заданного направления и замыканию его на стенку канала сопла. Напряжение на сжатой дуге составляет 60 200 В. Плотность тока сжатой дуги достигает 50 А/мм2, а удельная мощность достигает 2•106 Вт/см2. Плазменная среда оказывает значительное влияние на характеристики плазменной дуги. Условие выбора плазменной среды: она должна обеспечивать наибольшую удельную тепловую мощность при заданном расходе газа и затраченной электрической энергии, а также позволять сконцентрировать полученную энергию в тонкий плазменный шнур и сосредоточить ее на минимальном участке разрезаемого металла. Для плазменной резки применяют как однокомпонентные, так и многокомпонентные плазмообразующие среды. В плазменной горелке «Плазар» ГП02 в качестве плазмообразующей среды используется водяной пар, что улучшает санитарно – гигиенические характеристики процесса, обеспечивая простоту и надежность возбуждения дуги. Водяной пар образуется непосредственно в горелке из воды, которая в нее заливается перед началом работы.
2. Режимы резки.
Возможности аппарата «Плазар» АП 022 позволяют осуществлять ручную разделительную резку стальных листов толщиной 0,1 – 7 мм. Ориентировочные режимы разделительной резки металлов плазменной струей представлены в табл. 1. Результаты по скорости резки стали толщиной от 1 мм до 7 мм приведены в табл. 2, где скорость резания определялась по формуле:
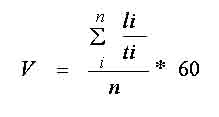 |
Где: V - скорость резания, мм/мин; l – длина реза, мм; t – время резания, с; n – число резов.
|
Определение скорости и качества разделительной резки плазменной струей аппарата проводилось на образцах листовых материалов различной толщины. Во всех случаях длина реза составляла 150 – 250 мм, а время резки фиксировалось при помощи секундомера с точностью до 1 секунды. Для проведения экспериментов были заготовлены образцы низкоуглеродистой стали Ст3 толщиной 0,8; 1,2; 1,5; 2,0; 2,6; 3,0; 4,0; и 5,0 мм, Ст20 толщиной 5,0; 6,0 и 7,0мм, нержавеющая сталь Х18НIОТ толщиной 1,2мм. и 3,0 мм. Образцы алюминиевых сплавов представляли собой листы толщиной 0,6; 1,2 и 4,0 мм. Кроме того, в работе была проведена резка медной фольги толщиной 0,4 мм. Во всех случаях ширина отрезаемых образцов для исключения влияния краевого эффекта была не менее 20 – 25 мм. Режимы резания выбирались по току в дуге 4 – 8А, напряжению на дуге 130 – 200 В.
Таблица 1.
Ориентировочные режимы разделительной резки плазменной струей.
Вид материала |
Толщина, мм |
Ток в дуге, А |
Напряжение на дуге, В |
Скорсть резки, мм/мин |
Черные, цветные металлы и сплавы |
< 1 |
4 |
130 – 150 |
500 – 650 |
Черные металлы и низколегированные сплавы |
2 – 4 |
6 |
170 – 180 |
100 – 250 |
Черные металлы и низколегированные сплавы |
4 – 5 |
7 |
190 – 200 |
50 – 80 |
Нержавеющая сталь типа 12Х18Н10T |
1 – 2 |
6 |
200 |
100 – 200 |
Алюминиевые и медные сплавы |
2 – 3 |
6 – 7 |
190 – 200 |
100 – 200 |
Ст. 20 |
5 - 6 |
8 |
190 - 200 |
45 - 35 |
Ст. 3 |
7 |
8 |
190 - 200 |
20 |
В результате проведенных экспериментов установлено, что скорость и качество резки исследованных металлических материалов толщиной 0,4 - 1,0 мм мало зависят от режимов резки и вида материала. Скорость резки составляет для алюминия толщиной 0,6 мм – 600-615 мм/мин, медной фольги толщ. 0,4 мм – 600-650 мм/мин, низколегированной стали толщ. 1,0 мм – 550-600 мм/мин. Уменьшение значения скорости разделительной резки нержавеющей стали толщ. 1,5 мм до 180 мм/мин обусловлено большой чувствительностью плазменной резки к толщине разрезаемого металла. При увеличении толщины разрезаемого металла до 2 мм влияние режимов резки приобретает существенное значение. Так при токе в дуге 5 А и при напряжении 170 В скорость резки алюминия составила 52 мм/мин, а при переключении на 7А (напряжение 140 В) скорость достигла 240 мм/мин. Эта закономерность прослеживается при резке сталей толщиной более 3мм. Анализ результатов резки металлов различной толщины позволяет предположить, что давление плазменной струи недостаточно для выдувания жидкой ванны при резке металлов большой толщины. Это предположение подтверждается тем, что при вертикальной или наклонной резке происходит вытекание расплавленного металла из реза.
Таблица 2.
Зависимость скорости резания от толщины листа низкоуглеродистой стали.
Толщинна листа, мм |
1 |
1,5 |
2,5 |
3 |
4 |
5 |
6 |
7 |
Скорость резания, мм/мин |
600 |
350 |
140 |
120 |
80 |
45 |
35 |
20 |
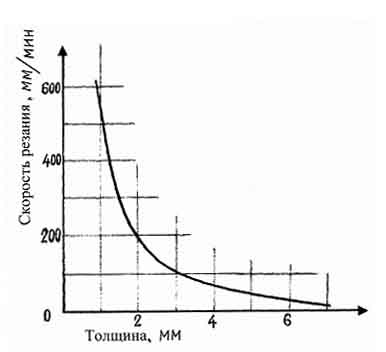 |
Рис.2 Качественная зависимость скорости резания от толщины листа низкоуглеродистой стали. |
На процесс плазменной резки оказывает влияние большое количество технологических факторов: сила тока и напряжение дуги, скорость резки, расход плазмообразующего газа, скорость его истечения из сопла, диаметр и длина канала сопла и др. В общем виде производительность процесса плазменной резки может быть представлена выражением
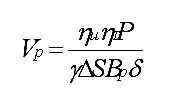 |
Где
– максимальная скорость резки, см/с;
– эффективный КПД плазменной дуги;
– термический КПД плазменной дуги;
– тепловая мощность источника нагрева, Вт;
– плотность разрезаемого металла, г/см3;
– средняя ширина полости реза, см;
– толщина разрезаемого металла;
– теплосодержание расплавленного металла, Дж/см3. |
Подогрев зоны реза перед резкой до температуры ~700 – 800°С обеспечивает разрезание металла с большей скоростью, более низкую шероховатость поверхности реза и умеренное наличие грата. Напряжение дуги определяют расход газа, диаметр и длина канала сопла (степень обжатия режущей дуги). В плазменной горелке «Плазар» ГП 02 для получения сконцентрированного столба дуги применена вихревая стабилизация дуги. Завихренный плазмообразующий газ обеспечивает надежность работы плазмотрона. Резку с использованием водяного пара осуществляют при избыточном давлении в резервуаре горелки ГП 02 0,05 – 0,08 МПа (0,5 – 0,8 ати). Давление газа зависит от сечения каналов завихрителя и сопла плазмотрона. Возбуждение дуги в горелке ГП02 происходит контактным способом в слабом потоке плазмообразующего газа, или в жидкой капле, замыкающей катод – анодное пространство. При запуске недозаправленной горелки иногда происходит обрыв малоамперной дуги. При слишком малом расходе газа плазменную дугу, горящую внутри горелки, не удается выдуть наружу из сопла. В этом случае температура плазменной струи не достигает максимального значения и эффективность резки снижается. После возбуждения дуги в плазменной горелке «Плазар» ГП02 происходит самосогласованное увеличение расхода плазмообразующей среды, что приводит к обжатию плазменного столба дуги. Напряжение на дуге при этом повышается, что, при крутопадающей вольт-амперской характеристике источника электропитания «Плазар» ИЭП2, равносильно увеличению мощности дуги. Аналогичное влияние на процесс плазменной резки оказывает увеличение длины канала сопла. При увеличении длины канала эффективность столба плазменной дуги возрастает и ширина реза по верхней и нижней плоскостям листа получается примерно одинаковая. Длина канала не должна превышать определенных пределов. Чрезмерное увеличение длины канала при заданном оптимальном его диаметре приводит к значительным потерям энергии на нагрев сопла. В плазменной горелке ГП02 имеет место оптимальное соотношение между диаметром канала сопла и его длинной. Техника резания аппаратом «Плазар» АП 022 имеет следующие специфические особенности:
- для правильного выбора режима резания необходимо наблюдать (следить) за факелом газов, выходящих за нижнюю плоскость листа;
- регулируя скорость перемещения горелки, добиваются выдавливания расплавленного металла из полости реза за нижнюю плоскость листа. Внешними признаками завышенной скорости резания являются выступившие на поверхность листа капли расплавленного металла или появление факела над поверхностью листа (если скорость перемещения превышает скорость выплавления и выдува металла).
При резке толстых (4, 5, 6, 7 мм) листов можно применить способ возвратно-поступательного движения горелки вдоль линии реза. Одним из внешних показателей режима резания является характер звучания плазменной струи. Все отклонения от нормального режима резания всегда сопровождаются изменением характера звучания плазменной струи. Величина напряжения на дуге выбирается исходя из толщины листа и требований, предъявляемых к качеству резки. Она регулируется изменением расстояния между катодом и соплом- анодом путем вращения регулировочной гайки на горелке. Начальную и конечную фазы резки выполняют с меньшей скоростью перемещения горелки, чем основную часть реза. Металлографические исследования кромок реза показали, что ширина его составляет 0,5 – 0,8 мм для стальных, алюминиевых и медных материалов толщиной менее 1 мм. При увеличении толщины стальных образцов до 5 – 7мм., ширина реза увеличивается до 1,5 – 2,2 мм. Ширина реза горелкой ГП02 зависит от суммарного воздействия ряда факторов: диаметра сопла, силы тока, скорости резки, расстояния от нижнего среза сопла до поверхности разрезаемого материала. Большое влияние оказывает диаметр сопла, определяющий сечение столба режущей дуги, т.е. для приближенных оценок ширину реза по верхней кромке можно принимать равной одному – двум диаметрам сопла. Для резки не с кромки, а с середины листа, а также при резке труб резка начинается с прожигания отверстия (с пробивки металла). Для прожигания отверстия необходимо горелку расположить под наклоном 45 - 60° к поверхности детали, а затем постепенно изменять угол резки до оптимального. Это позволяет исключить налипание брызг расплавленного металла на поверхность сопла. При резке стали толщиной 2 – 3 мм выдержка времени на пробивку составляет 2 – 4 с. Максимальная толщина стали, которую можно пробить без больших затруднений составляет около 6 мм. При необходимости пробивки металла большой толщины в начале реза можно просверлить отверстие диаметром 3 – 5 мм. Следует отметить, что напряжение на дуге используют для контроля за правильным протеканием процесса. Выход напряжения за заданные пределы сигнализирует о необходимости проверки отдельных составляющих процесса. Оценка качества реза производилась по внешнему виду по 4-х бальной системе: балл 3 означает отличную поверхность, балл 2 – хорошую, балл 1 – удовлетворительную, 0- при разделке металла на лом. Поскольку резка материала проводилась по линейке, зигзагов и выхватов на поверхности резов не обнаружено. Увеличение грата наблюдается при неравномерном перемещении плазмотрона на участках, резка которых производилась с большей скоростью. На листах из стали, алюминия и меди толщиной менее 1 мм незначительное количество грата имеется с нижней стороны реза. В целом при малых толщинах разрезаемого металла качество реза можно оценить в 3 балла. При резке алюминия толщиной 2 мм и стали толщиной 4 мм. качество реза оценилось в 1 балл, при резке стали толщиной 5 – 7 мм – 1 – 0 баллов. Подбирая скорость резания с учетом толщины детали и выбранной мощности дуги, можно значительно снизить образование грата и улучшить качество резов. Повышает производительность и качество реза использование шаблонов или лекал. На поверхности реза обычно образуются штрихи (бороздки), что является следствием непостоянства мгновенной скорости резки при определенной средней скорости резки. На рис.3 приведены фотографии поверхности реза стали толщиной 5 и 7 мм, а на рис.4 показано положение оси сопла горелки при разделительной резке. Общим для плазменной резки в различных плазмообразующих средах является образование у кромки реза зоны термического влияния (ЗТВ) с участками оплавления и структурных изменений в твердом металле. Допустимые значения протяженности зоны термического влияния для углеродистых сталей, отвечающие ГОСТ 14792 – 80, приведены в табл. 3.
Таблица 3.
Допускаемые значения протяженности зоны термического влияния, мм, для углеродистых сталей по ГОСТ 14792 – 80.
Класс |
Толщина разрезаемой углеродистой стали, мм |
5 - 12 |
13 - 30 |
31 - 60 |
I |
0,2 |
0,4 |
0,8 |
II |
0,8 |
1,6 |
3,2 |
III |
1,6 |
3,2 |
6,4 |
Глубина ЗТВ и соответственно отдельных ее участков при резке стали, выбранной марки и толщины, изменяется в зависимости от условий резки. С увеличением расхода газа, а также с уменьшением силы тока, зона уменьшается. Ширина, тип структуры, а также твердость ЗТВ при плазменной резке зависят от скорости охлаждения. Процессы плазменной резки вызывают насыщение кромок реза газами из атмосферы плазмы. Максимально насыщается газами литой участок зоны термического влияния.
a)
|
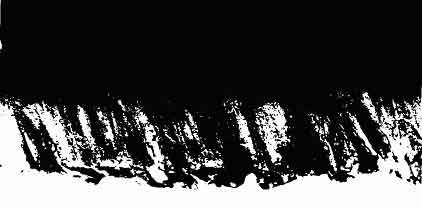 |
б)
|
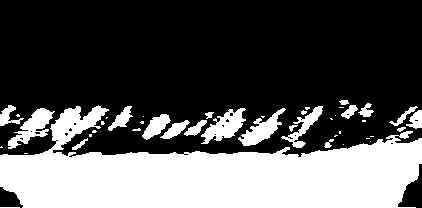 |
Рис. 3. Фотографии поверхностей реза стали 10 толщиной: а) – 7 мм и б) – 5 мм. |
3. Качество реза.
Качество реза характеризуется величиной образующегося грата, отклонениями перпендикулярности реза, шероховатостью, протяженностью зоны термического влияния и газонасыщенных кромок. На величину грата при плазменной резке оказывает влияние ряд технологических факторов: скорость резки, расход плазмообразующего газа, расстояние между плазмотроном и поверхностью разрезаемых листов и др. Для заданной силы тока существует диапазон скоростей, при которых грат минимален. Схематически это показано на рис. 5 [4]. Грат образуется как при малых скоростях (МС), так и на повышенных скоростях (ПС) резки. На рис. 5 заштрихована зона, в которой величина грата минимальна. Грат, образующийся при пониженных скоростях резки, легко удаляется с кромок реза. Удаление грата, образующегося при повышенных скоростях, является более трудоемкой операцией. С увеличением толщины металла скорость резки, при которой величина грата минимальна, уменьшается. С уменьшением расхода величина грата возрастает, что можно объяснить ослаблением механического воздействия плазменного потока на нижнюю кромку листа. Повышенное гратообразование наблюдают и при увеличении расстояния от плазмотрона до поверхности листа, особенно когда процесс резки осуществляют на скоростях, близких к предельно допустимым. В этих случаях применение устройств, поддерживающих расстояние между плазмотроном и разрезаемым листом, является обязательным. При плазменной резке ширина реза у верхних кромок больше, чем у нижних. С увеличением степени сжатия плазмы и уменьшением диаметра сопла плазмотрона уменьшается разница между шириной реза по толщине металла и неперпендикулярностью кромок. Величина неперпендикулярности кромок при плазменной резке представляет собой половину разницы ширины реза в верхней и нижней плоскостях разрезаемого листа. Скорость плазменной резки при прочих равных условиях оказывает существенное влияние на ширину реза и неперпендикулярность кромок. С увеличением расстояния от среза сопла до плоскости листа неперпендикулярность также возрастает.
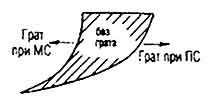 |
Рис. 5. Схема влияния скорости резки на образование грата [4]. |
4. Точность вырезки деталей.
Основными факторами, определяющими форму и размеры при термической резке, являются следующие: состояние исходного (разрезаемого) металла (чистота поверхности, химический состав, наличие расслоений, качество правки, размеры исходного листа); качество разметки, прямолинейность направляющих путей, форма и размеры детали (толщина, габаритные размеры, отношение длины к ширине, наличие или отсутствие вырезов); технология вырезки деталей, определяющая термические деформации (способ и режим резки, последовательность резки, наличие перемычек). Роль технологических факторов при резке определяется их влиянием на величину остаточных деформаций. При термической резке имеют место следующие виды остаточных деформаций: продольная деформация удлинения или укорочения; изгиб в плоскости вырезаемой детали. Наибольшее влияние на точность вырезки деталей оказывает изгиб деталей в плоскости и ее продольное укорочение. Изгиб детали особенно сильно проявляется при вырезке деталей большой длины, так как стрелка прогиба пропорциональна квадрату длины детали. Для снижения деформаций при термической резке следует придерживаться следующих рекомендаций: резку каждой детали начинать с кромки, имеющей наибольшую длину реза и расположенной у края листа, а заканчивать по короткой кромке с припуском; первыми вырезать, начиная от края листа, детали максимальных габаритов и требующие наиболее точного изготовления, а затем последующие ряды деталей в направлении противоположной кромки с сохранением принципа наибольшей жесткости для вырезаемой детали и исходного листа. Обеспечивать, по возможности, совмещение резов; отверстия в деталях выполнять до резки основного контура детали; при вырезке круглых деталей закреплять вырезаемые детали электромагнитными прижимами или заклинивать рез по мере выполнения резки для того, чтобы устранить смещение начала и конца ступеньки. С целью уменьшения величины деформации при резке деталей со сложным контуром, узких деталей большой протяженности, а также деталей, требующих высокой точности резки, желательно оставлять в листе непрорезанные участки (перемычки) с целью создания жесткого контура. Длина перемычки примерно равна толщине разрезаемого листа. На каждой детали оставляют не менее двух перемычек. Перемычки выполняют роль крепежа частично предупреждающего изгиб детали и ее продольное укорочение. Если деталь имеет сложную форму, то количество перемычек определяют приближенно по эквивалентному прямоугольнику, построенному на базе данной детали. Перемычки разрезают после вырезки всех деталей.
5. Санитарно – гигиенические характеристики процесса.
Обычная плазменная резка металлов имеет ряд недостатков: выделение аэрозоля, высокочастотный шум в комбинации с ультразвуком, электромагнитное излучение оптического диапазона (ультрафиолетового, видимого и инфракрасного) и ионизация воздуха. Особую опасность представляет аэрозоль, твердая составляющая которого состоит из соединений обрабатываемых металлов, а газовая – в основном из озона. Для удаления выделяющегося при резке аэрозоля и озона применяют вентиляционные системы. Вода в качестве плазмообразующей среды позволяет радикально улучшить санитарно -– гигиенические характеристики плазменной резки. Рекомбинация продуктов плазменной струи в водяной пар приводит к осаждению аэрозолей с конденсатом воды на поверхностях под обрабатываемой деталью. Источником шума и ультразвука при плазменной резке является плазменная горелка. Уровень шума зависит от режима резки, давления плазмообразующей среды, и практически для горелки ГП 02 не выходит за пределы допустимой нормы, которая составляет 80дВ. Источником электромагнитного излучения является плазменная дуга, расположенная внутри канала сопла, которая замыкается на наружную его обечайку в форме ярко светящегося ядра (жала). Излучение имеет максимальную направленность вдоль оси сопла от резчика и закрывается передней частью горелки, что позволяет исключить его вредное влияние на оператора. В общем случае должны быть выполнены требования по организации и оснащению соответствующих рабочих мест.
|